· case study · 4 min read
Better, faster data for certification experts
By using the Transsend platform to build its own smartphone apps, SGS was able to create tools to collect data in the field throughout New Zealand. Now the company's inspectors and engineers can carry out safety assessments on the spot and verify that correct processes have been followed.
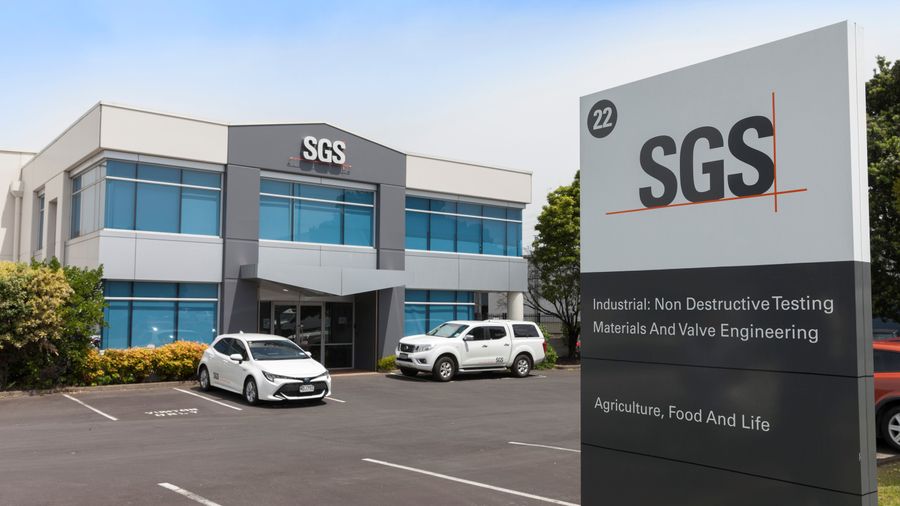
With annual revenue topping US$8 billion dollars, SGS is one of the world’s leading inspection, testing and certification companies. Accuracy and certainty are paramount to the people who work with this global industrial giant.
In New Zealand, SGS works across a range of sectors, from agriculture to manufacturing, providing companies with independent verification of their systems and processes. For New Zealand-based enterprises that have a boiler, a production line or a commercial building, there’s a good chance SGS is responsible for their annual inspection and certification.
The SGS New Zealand operations revolve around hundreds of field visits every day from over 600 staff based at 25 locations around the country. Since safety is central to the company’s mission, SGS takes great care to ensure risks are always managed appropriately.
The company historically used an array of paper forms to ensure correct processes were followed before, during and after each site visit. This information had to be collected from field employees and then individually scanned before being entered into the SGS computer system by back office staff. It was a slow and cumbersome system, with the potential for transcription errors to creep in.
Dean Currie, the SGS General Manager of Industrial Non Destructive and Materials Testing in New Zealand, wanted to speed up the collection of critical data while also minimising errors.
“Data from field visits was being entered right at the end of the process. It might be two weeks after one of our inspectors stepped onto a client’s site before we had the full picture. That made it hard for us to ensure correct processes were being followed.”
The advantages of an app
By using the Transsend platform to build its own smartphone apps, SGS is able to create tools to collect data in the field throughout New Zealand. Now the company’s inspectors and engineers can carry out safety assessments on the spot and verify that correct processes have been followed.
Within minutes this data is sent via the mobile phone network to Transsend servers where it is converted into Word documents and then directed to SGS users. It can be directly entered into the SGS system with no need for double handling or transcription.
“For us, it’s all about capturing the data once and then getting it to the right people without delays and errors,” says Dean. “We have up to 200 inspectors and technicians in the field at any one time, so we’re generating hundreds of reports each day. Transsend has enabled us to automate this critical part of our process.”
Better reporting means safer staff
Dean has also used the Transsend platform to create an incident reporting tool that keeps managers aware of accidents and near misses in real time.
“If one of our engineers twists an ankle during a site visit, we need to be aware of it. Maybe there’s been an increase in one hazard on certain sites, and this needs to be evaluated so we can instigate the right measures. We need timely alerts rather than relying on phone calls and text messages at a later stage. By using the Transsend tools to build our own app we can get early notification into our system. And we can act appropriately.”
The tools to build your own digital apps
With the Transsend platform, Dean and his team have the power to create their own apps in-house.
“The beauty of the Transsend system is that we don’t have to hire software developers at $200 an hour to code each app,” he says. “If there’s a business process I want to turn into a mobile tool, I can create a new app in 30 minutes. I could have it up and running within hours, available for our guys to use on their smartphones.”
“Having the ability to create our own apps has helped us ensure safety, drive efficiency and provide a better service to our customers every day.”
Executive summary
SGS is a global leader in testing and certification. Its New Zealand operations involve over 600 staff performing hundreds of site visits every day.
Adhering to safety procedures previously required an array of paper forms and back-office data entry processes that lagged weeks behind each inspection.
SGS converted its safety procedures into smartphone apps for workers to use in the field, with data sent to SGS via the Transsend server.
Safety reports complied in the app are automatically converted into standardised Word docs for accessibility by SGS managers and clients as required.
The process captures data from field staff at source and ensures it is entered without transcription errors.
SGS has also created a Transsend app for incident reporting, enabling real time notification of accidents and near misses so appropriate measures can be taken.
The Transsend platform provides tools for SGS to create their own apps with no technical input. Managers build digital tools and deploy them within hours, without the need of software developers.